La méthode Kaizen en amélioration continue ?
En amélioration continue, la méthode Kaizen vise à optimiser la productivité d’un processus industriel par de petites améliorations régulières. Elle cherche à enclencher un changement positif et progressif pour améliorer la performance industrielle.
La méthode d’amélioration continue Kaizen : Définition
La méthode Kaizen, née au Japon dans les usines Toyota dans les années 50, est une philosophie de gestion qui se concentre sur l’amélioration continue de la qualité, de l’efficacité et de la productivité d’un processus ou d’une entreprise.
Aussi, la philosophie de la méthode Kaizen est basée sur l’idée que de petites améliorations régulières peuvent avoir un impact significatif sur la qualité et l’efficacité d’un processus ou d’une entreprise.
Origine et philosophie du Kaizen
Le mot « kaizen » se compose de deux mots japonais : « Kai », qui signifie « changement », et « Zen », qui signifie « bon ». La philosophie de la méthode Kaizen consiste à rechercher constamment des moyens d’améliorer les processus, les produits et les services d’une entreprise. Ceci afin d’atteindre des niveaux de qualité et d’efficacité plus élevés.
La méthode Kaizen est le concept le plus important du management japonais. Elle est alors la clé de la compétitivité du modèle japonais au XXème siècle.
La philosophie Kaizen favorise les petits changements rapides et réguliers. Elle s’oppose alors à la méthode radicale traditionnellement utilisée en entreprise, le reengineering (gros changements, recherche d’innovations de rupture du processus industriel).
La méthode Kaizen met l’accent sur la participation de tous les membres de l’équipe pour trouver des solutions aux problèmes et pour identifier les opportunités d’amélioration. Elle encourage également la communication ouverte et la collaboration entre les membres de l’équipe pour renforcer l’engagement et la motivation des employés.
Les grands principes de la méthodes Kaizen
Comme nous l’avons vu précédemment, la méthode Kaizen n’est pas un outil défini. Elle s’apparente plutôt à un état d’esprit du Lean Manufacturing, une façon d’agir et de penser dans l’atelier.
La méthode Kaizen est donc une philosophie qui repose sur plusieurs principes :
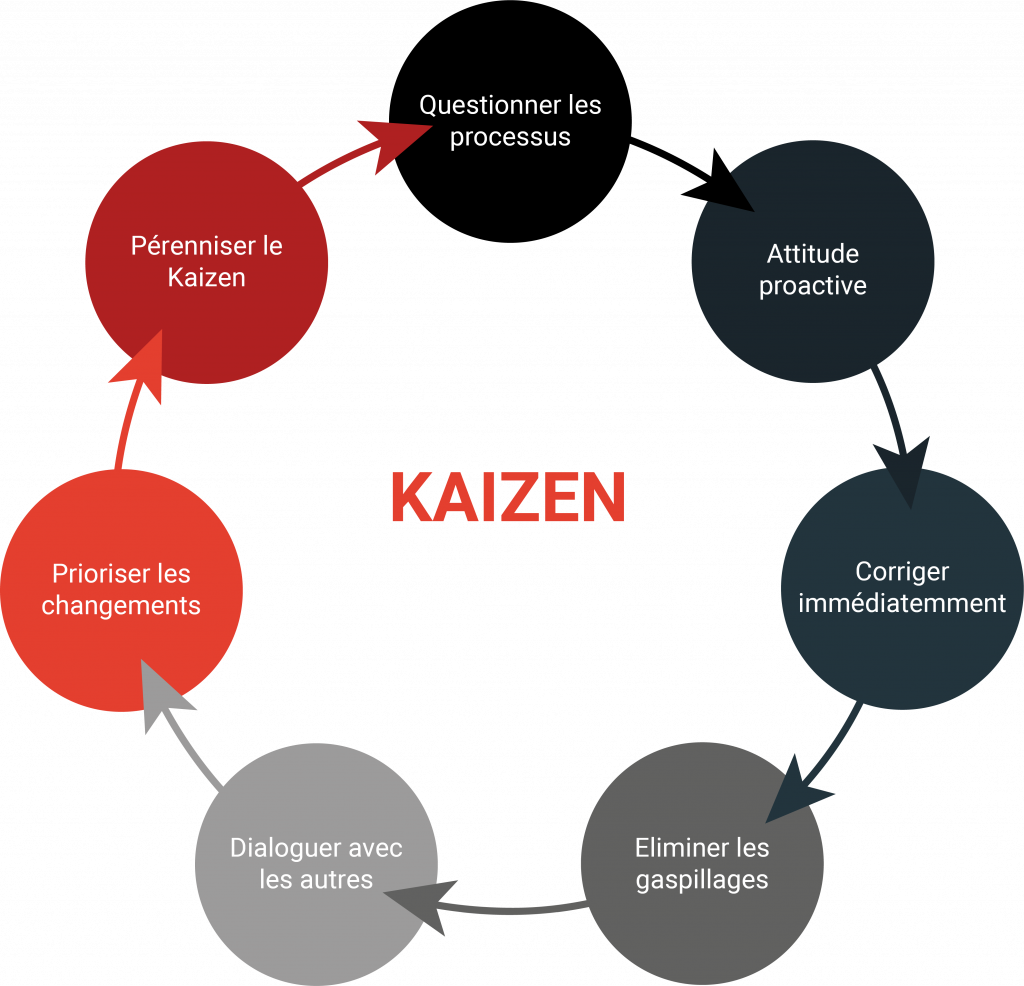
Remettre sans cesse en question les méthodes de travail
Le premier principe de la méthode Kaizen, sur lequel repose tous les autres, est de considérer qu’il est toujours possible de mieux faire. Il faut ainsi être prêt à remettre en question la manière de fonctionner, les processus, les objectifs.
Autrement dit, ne pas hésiter à questionner un processus qui semble fonctionner.
Adopter une attitude proactive
Être réactif face aux problèmes rencontrés dans un atelier est déjà une première étape. Mais il est nécessaire d’être aussi proactif. Être proactif c’est chercher en permanence la meilleure organisation. C’est identifier en amont les faiblesses, mieux prévoir, planifier, et donc, organiser les processus.
Traiter et corriger les erreurs immédiatement
Ne pas attendre que les erreurs s’accumulent pour les corriger. Parce que les identifier rapidement c’est bien, mais les traiter immédiatement c’est mieux. En respectant ce principe, on évite finalement d’aggraver certaines erreurs et leurs conséquences sur la production.
Il existe tout de même des méthodes très efficaces d’amélioration continue pour réduire et éliminer les erreurs, comme la démarche Poka Yoke.
Prioriser les changements
Pour rappel, le Kaizen (et donc l’amélioration continue), favorise les changements dits de « petits pas ». Ainsi pour chaque changement, il est important de prioriser les plus rapides à mettre en place, ceux qui nécessitent le moins de ressources, et ceux qui ont un maximum d’impact pour un minimum d’effort.
Dialoguer et échanger avec les autres
Face à une situation complexe ou une décision importante, il est bon de consulter l’avis d’experts ou de personnes susceptibles de pouvoir apporter une solution nouvelle. En faisant cela, on s’assure d’enrichir notre réflexion et de prendre en considération de nouveaux avis.
Eliminer les gaspillages : Muda, Mura, Muri (3M)
L’élimination des gaspillages est une notion primordiale de l’amélioration continue et du Kaizen. C’est pourquoi les industries japonaises (parentes de l’amélioration continue), mettaient tout en œuvre pour éliminer ces trois types de gaspillages (3M) :
- Muda :
Muda signifie gaspillage. Les gaspillages Muda sont liés aux activités qui n’apportent aucune valeur ajoutée. Mais il est généralement possible d’automatiser ce type de gaspillage.
Exemple : A chaque fin de cycle, un opérateur doit se déplacer dans tout l’atelier pour accéder au stock et transporter la matière nécessaire sur son poste. - Mura :
Mura signifie irrégularité. Les gaspillages Mura sont liés à l’incapacité de rendre une production stable et régulière. Il est nécessaire que chaque flux de travail s’écoule de manière fluide.
Exemple : Sur une chaîne de fabrication, la capacité d’un poste est supérieure à celle du poste suivant. Il y a donc la création d’un goulot d’étranglement. - Muri :
Muri signifie surcharge. Les gaspillages Muri sont liés à l’utilisation surdimensionnée ou sous-dimensionnée d’un moyen par rapport au besoin. Ils peuvent désigner également une surcharge physique des opérateurs, des difficultés techniques rencontrées.
Exemple : Un opérateur n’est pas suffisamment formé pour accomplir la tâche demandée, il passera plus de temps à accomplir cette tâche
Pérenniser la philosophie Kaizen
Enfin, le principe fondamental de toute la philosophie Kaizen. Ce qui rend possible l’amélioration continue, c’est la pérennisation de tous ces principes.
L’utilité de faire de « petites améliorations ayant le plus gros impacte » est qu’elles sont plus faciles à mettre en place, mais surtout à pérenniser dans le temps. Cela évite l’effet « YoYo ».
Les avantages de la méthode Kaizen dans votre atelier industriel ?
Adopter la méthode Kaizen dans un atelier industriel, c’est améliorer l’ensemble du processus et tendre vers une production optimale sans perte. Tout en augmentant la productivité globale.
Améliorer la qualité de la production
La recherche incessante de perfectionnement des processus induit forcément une augmentation de la qualité finale des produits. Cela peut se traduire de deux manières :
- Premièrement, une augmentation radicale du Taux de qualité. Vous constatez alors une forte baisse des rebuts et des gaspillages matière dans votre processus.
- Deuxièmement, de manière globale, la production est de meilleure qualité et vous touchez de nouveaux clients.
Améliorer la disponibilité et les délais de production
La proactivité des équipes aide à anticiper les futurs défaillances et ainsi réduire le taux de panne. De plus, l’optimisation et la réduction de tous les temps « morts » (réglage, réassort matière, maintenance, panne,…) libère un temps considérable et engage vos moyens sur une période plus longue.
L’ensemble des équipements sera mis à contribution de manière optimale. Ainsi, les délais de production seront réduits en vue d’atteindre des objectifs plus élevés.
Améliorer la performance et la cadence des moyens
Un processus bien étudié, bien réorganisé avec des plans d’action précis et concrets vous permet d’optimiser la performance de vos moyens. Le résultat ? Avec le même engagement des moyens, vous produisez plus.
Notons que l’augmentation d’au moins l’un de ces trois taux (taux de qualité, taux de disponibilité et taux de performance) impacte positivement le Taux de Rendement Synthétique (TRS), et donc l’efficacité globale de vos moyens de production.
Enfin, améliorer les conditions de travail et l’implication des opérateurs
Le Kaizen, ou l’amélioration continue de manière générale, ne peut connaître de succès sans une adhésion totale de l’ensemble des salariés. Mais en réorganisant de manière optimale l’atelier, on améliore les conditions de travail et l’implication des opérateurs.
Les opérateurs sont au premier plan pour identifier ce qui fonctionne et ne fonctionne pas. Ils sont alors la première force de proposition pour mener des plans d’action. Servez-vous de leur connaissance et de leur proximité terrain pour échanger sur le processus et les axes d’améliorations.
Comment mettre en place la méthode Kaizen dans votre atelier ?
4 exemples d’outils de la méthode Kaizen :
1 La méthode 5S
La méthode 5S est une technique de gestion de la qualité et de l’efficacité qui permet d’optimiser l’environnement de travail. Pour cela, il est important de nettoyer, ranger et organiser efficacement l’espace de travail.
La méthode 5S est une méthode japonaise qui a été mise au point dans les années 1960 pour améliorer la qualité des produits fabriqués par les entreprises japonaises. Depuis, elle a été adoptée par des entreprises du monde entier pour améliorer leur efficacité et leur productivité.
- Seiri (dégagement). Trier et se débarrasser de tout ce qui n’est pas nécessaire dans l’espace de travail, afin de libérer de l’espace et d’éviter les encombrements.
- Seiton (ordre). Ranger et organiser les éléments restants afin de les rendre facilement accessibles et d’éviter les pertes de temps et les erreurs.
- Seiso (nettoyage). Nettoyer régulièrement l’espace de travail afin d’éviter les contaminations, les accidents et pour maintenir un environnement de travail agréable et sûr.
- Seiketsu (standardisation). Définir des normes et des procédures afin de maintenir les trois premiers S (Seiri (dégagement), Seiton (ordre) et Seiso (nettoyage)) en place de manière régulière et efficace.
- Shitsuke (discipline). Faire de la méthode 5S une habitude quotidienne en la pratiquant de manière continue, en surveillant les résultats et en les améliorant en permanence.
2 La méthode PDCA (roue de Deming)
La roue de Deming, également connue sous le nom de cycle PDCA, est une méthode de gestion de la qualité qui a été développée par W. Edwards Deming, un statisticien et consultant en gestion.
Cette méthode se compose de quatre étapes : Planifier, Exécuter, Contrôler et Agir (PDCA – Plan, Do, Check, Act). Elle se base sur le principe de l’amélioration continue et aide les entreprises à s’adapter aux changements dans leur environnement.
La première étape du cycle est la planification (Plan). Dans cette étape, les entreprises définissent leurs objectifs et établissent un plan pour atteindre ces objectifs. Les étapes de planification comprennent la définition des objectifs, l’analyse des données et la mise en place d’un plan d’action.
La deuxième étape du cycle est l’exécution (Do). Dans cette étape, les entreprises mettent en œuvre le plan qu’elles ont élaboré lors de l’étape de planification. Les étapes de l’exécution comprennent la mise en place des processus, la formation des employés et la gestion des ressources.
La troisième étape est le contrôle (Check). Dans cette étape, les entreprises s’assurent que tout s’est bien passé, et relève tous les éléments à améliorer.
Enfin, la quatrième et dernière étape consiste à agir ou ajuster (Act). Une fois avoir contrôlé et analysé les résultats des actions mises en place, prenez de nouvelles dispositions pour améliorer votre processus, et planifiez-les, réalisez-les, contrôlez-les, et recommencez.
3 La méthode des 5 pourquoi
La méthode des 5 pourquoi est une technique d’analyse de la cause racine. Elle consiste à poser cinq fois la question « pourquoi » pour comprendre l’origine d’un problème. Cette méthode a été développée par Sakichi Toyoda, fondateur de Toyota Industries dans les années 1930.
En quoi consiste la méthode des 5 pourquoi ?
La méthode des 5 pourquoi aide les professionnels de l’industrie à identifier la cause profonde d’un problème. Elle consiste alors à poser la question « pourquoi » à chaque étape de l’analyse, en se demandant pourquoi le problème s’est produit.
Prenons l’exemple d’une entreprise de production qui rencontre des problèmes de qualité avec un produit particulier. Les étapes suivantes peuvent être suivies pour résoudre le problème :
- Première question, Pourquoi la qualité du produit est-elle mauvaise ? (réponse, parce que la machine ne fonctionne pas correctement)
- Deuxième question, Pourquoi la machine ne fonctionne pas correctement ? (réponse, parce que le lubrifiant de la machine n’est pas de qualité suffisante)
- Troisième question, Pourquoi le lubrifiant n’est pas de qualité suffisante ? (réponse, parce que le fournisseur du lubrifiant n’a pas respecté les spécifications de qualité)
- Quatrième question, Pourquoi le fournisseur n’a-t-il pas respecté les spécifications de qualité ? (réponse, parce que l’entreprise n’a pas clairement communiqué ses spécifications de qualité au fournisseur)
- Cinquième question, Pourquoi l’entreprise n’a-t-elle pas clairement communiqué ses spécifications de qualité au fournisseur ? (réponse, parce que le processus de communication entre l’entreprise et le fournisseur manque de précision)
En utilisant cette méthode, l’entreprise a pu découvrir la cause racine du problème et prendre des mesures pour améliorer son processus de communication avec ses fournisseurs. Cela a permis d’éviter que le même problème ne se reproduise à l’avenir.
4 La méthode Kanban
Introduite elle aussi dans les années 50 chez Toyota, la méthode Kanban se base sur deux principes : le visuel et le temps réel.
Cette révolution méthodologique prévoit une production basée sur la demande plutôt que sur l’offre. En d’autres termes, une entreprise ne produit plus de stock qu’elle cherche à écouler, elle produit en fonction des commandes qu’elle reçoit.
Pour répondre au changement d’organisation imposé par le Kanban, il prévoit une méthodologie à appliquer. Son fonctionnement est basé sur une meilleure organisation et communication entre les services et les opérateurs.
Pour cela, à chaque nouvelle commande une étiquette (Kanban en japonais) est créée et collée sur un tableau. Elle indique la tâche ou opération à réaliser, une date de fin, et en fonction de son évolution peut être déplacée dans les colonnes « à faire », « en cours », « terminé »…
Cette technique permet de visualiser de manière claire toute les étapes de la chaîne de production, ainsi que l’avancement des tâches, en identifiant rapidement les points de blocage.
Application de la méthode Kaizen avec le logiciel MES Aquiweb
Support de mise en place d’une démarche d’amélioration continue, le logiciel MES Aquiweb dispose de fonctionnalités dédiées aux techniques les plus utilisées dans les sites industriels.
Définir les objectifs d’amélioration
Avant toute chose, la première étape est de définir les objectifs d’amélioration. Il est important de définir clairement les objectifs que vous souhaitez atteindre grâce à la méthode Kaizen et le logiciel MES Aquiweb. Ces objectifs doivent respecter la méthode SMART. Ils doivent être :
- Spécifiques : Définition et personnalisation d’un objectif spécifique par rapport au travail et à la personne en charge de cet objectif.
- Mesurables : un objectif mesurable est clairement quantifiable par des chiffres précis à atteindre.
- Acceptables : un objectif acceptable est atteignable compte tenu des moyens octroyés pour sa réussite.
- Réalistes : un objectif réaliste (à ne pas confondre avec acceptable), est un objectif pertinent qui sera assimilé par la personne concernée.
- Temporaires : un objectif temporaire est défini dans le temps et doit avoir une date limite.
Servez-vous des données collectées par le logiciel MES pour analyser, quantifier et mettre en place ces objectifs.
Aquiweb, support des méthodes Kaizen
Méthode 5S
Pour rappel, la méthode 5S se réalise sous forme de tâche, et a pour objectif de construire un environnement de travail fonctionnel.
A travers des fonctionnalités dédiées, le logiciel MES Aquiweb dématérialise le support de suivi des actions 5S.
Ainsi, le manager définit le planning des actions, consulte en temps réel le suivi et la réalisation des actions, et utilise le logiciel comme support d’analyse.
L’opérateur lui, dispose directement sur son poste opérateur du planning des actions 5S avec des alertes visuels, d’un planning d’entretien et d’un support sous forme de checklist des actions à réaliser.
SMED
La méthode SMED est une méthode de changement rapide d’outil qui a pour objectif d’augmenter la flexibilité de la production.
Aquiweb mesure automatiquement les temps de changements, et alerte l’opérateur lorsqu’une action SMED est nécessaire. C’est pourquoi le logiciel fournit des indicateurs temps réel pour les managers et opérateurs pour suivre la progression du SMED sur le long terme.
Management visuel
Le management visuel est très important dans le succès d’une démarche Kaizen. Il facilite la réactivité des opérateurs et managers en étant au plus près du terrain, il aide à la pris de décision, et clarifie la définition des objectifs sous formes d’éléments graphiques et visuels.
Aquiweb diffuse de manière dynamique les données à valeur ajoutée sur différents supports numériques (écrans TV, smartphones, tablettes…). L’intérêt d’un tel outil est l’immédiateté de la prise d’information et sa diffusion.
Formation des équipes
Formez vos équipes au méthodes Kaizen grâce au management visuel et aux instructions au poste.
La méthode Kaizen nécessite l’implication de tous les membres de l’organisation, et il est important de former les équipes aux méthodes Kaizen pour qu’elles soient proactives sur les améliorations de processus, qu’elles sachent comment utiliser le logiciel MES pour collecter les données, faire des progrès et les quantifier.
Suivi de la production
Collecte des données en temps réel
Le logiciel MES collecte les données en temps réel sur les processus de production, les temps d’arrêt, les erreurs de production, etc. Aussi, cette collecte de données favorise l’identification des zones qui nécessitent des améliorations et fournit une base solide pour mesurer l’impact des changements apportés.
Une collecte précise des données suivie d’une analyse complète sont deux étapes très importantes dans la méthode Kaizen, car elles apportent de la visibilité sur les points d’actions, les axes d’améliorations, savoir si une action est terminée ou pas…
Analyse des données
Une analyse des données collectées dans le logiciel MES (via le Pareto des causes de perte par exemple) permet d’identifier les causes profondes des problèmes rencontrés dans l’atelier et de trouver des opportunités d’amélioration. Ces analyses sont facilitées par des outils d’analyses graphiques intégrés au logiciel Aquiweb.
Mise en place des actions d’améliorations
Une fois les données de votre atelier collectées et analysées, mettez en place des plans d’actions clairs. Ces plans peuvent s’appuyer sur diverses fonctionnalités d’Aquiweb, comme des checklist OK démarrage, des actions SMED, 5S, un contrôle qualité rigoureux etc…
Suivi du progrès
Enfin, dans une démarche Kaizen, l’ensemble des acteurs doit suivre régulièrement les progrès et améliorations mis en place.
Sur le logiciel MES, le manager peut créer et diffuser des tableaux de bord qui retranscrivent de manière claire les données de production, et les données spécifiques aux méthodes Kaizen (5S, SMED, Pareto,…). Il s’assure ainsi que les équipes s’impliquent, et que les objectifs d’amélioration sont atteints et que les résultats soient durables.