Pourquoi intégrer un logiciel MES dans votre atelier industriel ?
La transformation numérique de l’industrie ne fait désormais plus débat et est aujourd’hui indispensable pour pérenniser la compétitivité des entreprises. Le logiciel MES est aujourd’hui la solution qui s’impose pour mieux piloter l’usine et entrer dans la digitalisation. Voici les 6 bonnes raisons de faire entre le MES dans vos ateliers.
Raison 1 – Pour transformer l’atelier et optimiser la production
Vous le savez tous, sans informatique dans l’atelier, le papier est omniprésent pour piloter, pour suivre, pour animer et pour gérer.
1.
Piloter
De nombreux documents sont imprimés depuis l’ERP et d’autres systèmes pour être distribués dans l’atelier : bon de travail, documentation technique, dossier d’OF.
2.
Suivre
Les opérateurs déclarent manuellement leur production sur des documents : relevés de temps, de quantité, fiches de qualité, fiches d’incidents, causes des arrêts, déclaration de consommation. Pourtant, les opérateurs sont payés pour produire, non pas pour faire des tâches administratives à non-valeur ajoutée.
3.
Animer
Les managers ont besoin de données pour animer leurs réunions d’équipe notamment lors des point AIC (Animation par Intervalle Court). Pour cela, il faut collecter les fiches papiers, consolider les données, souvent sous Excel, pour calculer les indicateurs clés de productivité et de performance. Puis il faut reporter toutes ces informations sur les tableaux flash d’animation. Collecte, consolidation manuelle, calcul… autant de tâches supplémentaires sans intérêt qui n’apportent pas de valeur
4.
Gérer
La plupart de ces données doivent être ressaisies dans l’ERP, pour clore les OF notamment, suivre les stocks… On étudie les temps passés, les consommations, les quantités produites, les résultats… Tout un ensemble d’actions manuelles qui consomment beaucoup de temps et peuvent être remplacées.
Le logiciel MES fluidifie les échanges en temps réel. Le MES distribue les données de gestion dans l’atelier depuis l’ERP. Il collecte les informations du terrain (produits, rebuts, qualification des arrêts…) par connexion directe aux équipements et par des terminaux fixes ou mobiles auprès des opérateurs. Une fois les données à disposition, il les consolide pour les mettre à disposition des acteurs de la production en temps réel. L’opérateur au pied de la machine suit sa cadence de production en temps réel. Il est alerté en cas d’aléas. Ensuite pour le manager qui peut réagir et anticiper les aléas plutôt que constater et mettre des actions correctives à posteriori.
Raison 2 – Pour garantir la continuité numérique
Le rôle du logiciel MES est de garantir la véracité de la donnée tout au long du flux industriel, malgré les nombreux échanges et transferts qui existent partout dans l’usine : on appelle cela la continuité numérique.
Dans la cartographie du système d’information industriel (SSI), on distingue différents systèmes applicatifs (souvent des logiciels) qui répondent à des besoins précis : ERP (gestion globale), PLM (gestion des produits), WMS (gestion de l’entrepôt logistique), GMAO (gestion de la maintenance)… Au cœur de l’atelier, le seul système qui se focalise uniquement sur les problématiques des acteurs opérationnels est le MES. Quelle est l’interconnexion entre ces différents systèmes ?
1. L’ERP, en charge de la gestion globale de l’usine, va « redescendre » au MES les OF, les références et les quantités à produire notamment. De son côté, le MES va suivre l’exécution de la production auprès des opérateurs et des équipements. Il transmettra à l’ERP les résultats de production (temps, quantité, consommation…)
2. Le PLM transmet au MES les données techniques liées aux produits : modes opératoires, documentation, nomenclature théorique… en retour le MES lui renvoie les données de l’exécution : nomenclature réelle, déroulé de l’exécution. De son côté, le PLM pourra effectuer des mises à jour auprès de l’ERP (nomenclature, gestion du changement, gamme…)
3. La GMAO reçoit les données de production collectées et consolidées par le MES. La GMAO va ainsi gérer les besoins et les interventions de maintenance de manière anticiper. De son côté, le logiciel MES se base sur les plans de maintenance de la GMAO pour alerter les opérateurs et les équipes maintenance au bon moment. Par son ordonnancement connecté, le MES peut informer de manière précise les équipes sur leurs créneaux d’intervention ou de correction des pannes.
4. Le WMS échange avec le MES afin de connaitre les produits finis réalisés et ainsi gérer les entrées en stock dans l’entrepôt par exemple. Le WMS prendra quant à lui le relai sur la partie management et optimisation des stocks dans l’entrepôt.
Raison 3 – Pour faciliter l’analyse de la performance
Le calcul d’indicateurs comme le TRS est essentiel pour faciliter le suivi de production. Il indique la productivité d’un atelier, d’un équipement, d’un opérateur… en prenant en compte trois composantes : la disponibilité des équipements, la performance (machine ou opérateur), et la qualité produite.
Traditionnellement, les informations de production (quantité, temps d’arrêts…) sont relevées manuellement et à postériori. Aussi, elles sont souvent entachées d’imprécisions voire d’erreurs car leur renseignement constitue une charge supplémentaire pour les opérateurs. Les managers doivent saisir ces informations dans des tableaux Excel, faire des calculs, en vérifier l’exactitude.
De fait, les résultats parviennent en différé : l’équipe où le problème est survenu n’est plus présente. Il faudra attendre peut-être la semaine suivante pour essayer de comprendre les causes, et tenter d’y remédier.
Le MES va fournir en temps réel les informations d’arrêts ou de problèmes qualité, ce qui va permettre de réagir tout de suite en cas de problème, ou au moins de le comprendre. Des actions correctives seront mises en place dans les prochaines heures.
Les résultats ne sont pas sous forme papier, mais en base de données. Il est facile de comparer les résultats à ceux des semaines précédentes et d’en tirer les enseignements. L’industriel dispose d’une mine d’informations qui pourra l’aider dans l’amélioration continue de la production.
Les outils d’analyse proposés par le MES permettent de croiser l’information, de la visualiser sous l’angle produit, outil, machine, personne, opération. Tout cela sans effort. Il permet aux managers de bâtir et suivre des plans d’actions plutôt que de consolider des données.
Une performance mesurée et analysée en temps réel pour une performance augmentée !
Raison 4 –Pour faciliter la traçabilité des flux de matières dans l’usine
Très répandue dans certaines industries (automobile, aéronautique, pharmaceutique, agroalimentaire), la traçabilité est souvent vécue comme une contrainte réglementaire ou une contrainte des donneurs d’ordre. Au-delà de la gestion des plans de rappels, si vous l’utilisiez à des fins d’optimisation de la production ? C’est ce que propose le logiciel MES.
Il garantit la bonne exécution et la bonne répétabilité des process : détrompage (vérification des composants de la nomenclature), suivi des validations d’étapes…Il assure aussi la qualité des produits en proposant des outils SPC pour suivre les dérives qualité et mettre en place des actions correctives. Par une gestion en temps réel, il permet aussi l’identification et de résolution des problèmes.
Mais assurer une traçabilité interne c’est aussi gérer la complexité de conserver un suivi total, de la réception à l’expédition (on parle de traçabilité « Dock to Dock »), avec des milliers de données, tout en respectant les exigences clients et réglementaires en constante évolution. Là aussi le logiciel MES apportera toute la puissance de l’outil informatique pour faciliter cela.
Le logiciel MES permet une traçabilité totale et en temps réel des flux de matières dans l’usine. Il limite considérablement le papier dans l’atelier et peut aussi garantir une traçabilité du process.
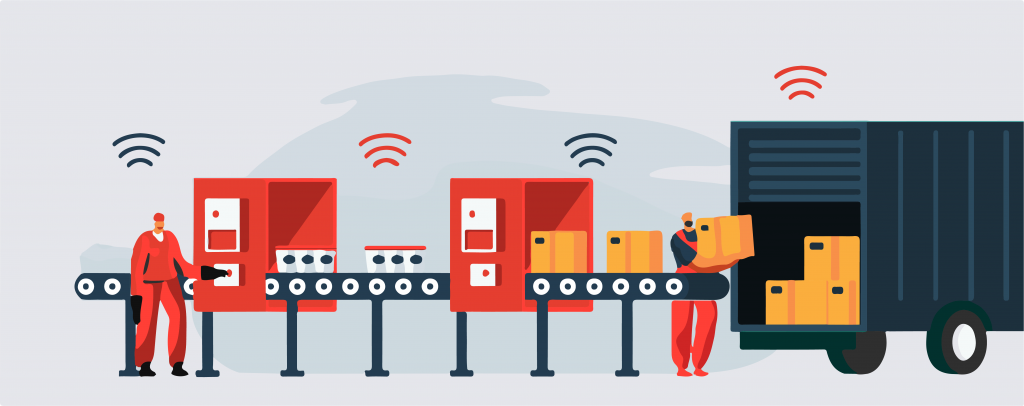
Raison 5 – Pour améliorer la communication dans l’atelier
La communication est omniprésente dans l’atelier. Qu’elle soit à ascendante, descendante ou transversale : elle doit être facilitée pour garantir l’augmentation de la productivité dans l’atelier.
L’activité de l’usine génère un grand nombre d’informations. Les acteurs de l’atelier partagent ces dernières en temps réel. Les niveaux d’informations sont différents en fonction du rôle de chaque intervenant dans l’usine : les opérateurs ont accès aux données opérationnelles nécessaires pour leur production, les managers ont accès à des tableaux de bord de gestion et aux outils d’amélioration continue, la direction dispose d’une vision macro et financière de l’activité de l’usine.
Au-delà de position hiérarchique, il s’agit aussi d’une question de métier : la production va partager les données avec d’autres services (qualité, maintenance, méthode, logistique, gestion) qui eux, vont les exploiter de manières différentes.
Le logiciel MES digitalise toutes les données pour les partager à la bonne personne et au bon moment sous forme d’alerte (notification, email, alerte visuelle…), de tableau de bord web, rapports… Il propose aussi sur grand écran des tableaux flash pour l’AIC. Le manager anime ces points d’information quotidien sur différents thèmes : performance, sécurité…
On peut aussi trouver dans l’atelier des affichages TV avec des indicateurs graphiques : animation automatique par des graphiques, des couleurs ROUGE/VERT, des pictogrammes d’alertes visuels, la position en % de l’objectif… Le management visuel fluidifie et optimise cette communication.
Raison 6 – Pour se lancer dans « l’Industrie du Futur »
L’engagement vers l’industrie du futur est le défi des entreprises industrielles. Elles se tournent de plus en plus vers des organisations agiles, connectées & optimisées pour augmenter leur compétitivité et leur flexibilité.
De nombreuses organisations mènent des initiatives de transformation vers l’usine 4.0. Souvent à l’initiative de la direction, des organismes externes (publics ou privés) peuvent financer ces projets.
Cette transformation digitale ouvre la voie à une nouvelle révolution industrielle avec comme chef de fil le logiciel MES. Au cœur du dispositif de l’usine du futur, il digitalise les opérations de production. Il soutient les opérateurs dans leurs activités et optimise les démarches d’amélioration continue menées par le management pour gagner en performance. Il est le chef d’orchestre qui harmonise les échanges entre les différentes composantes de l’industrie 4.0.
Des industriels témoignent : gain de performance et bien être
Alors patron de PME, directeur d’usine, responsable de production et ingénieur amélioration continue : entrez facilement dans l’industrie du futur avec le logiciel MES. Découvrez une organisation plus flexible, plus compétitive, plus respectueuse de l’environnement et au plus proche des préoccupations des hommes !